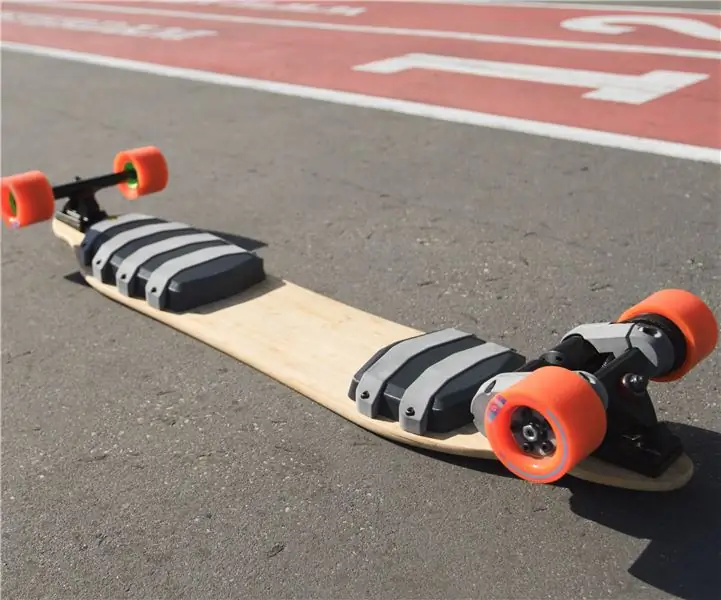
Sisällysluettelo:
2025 Kirjoittaja: John Day | [email protected]. Viimeksi muokattu: 2025-01-23 14:44
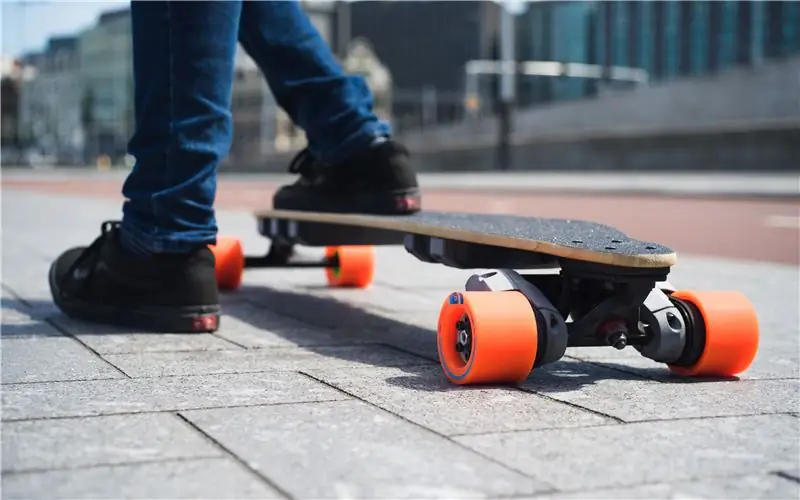
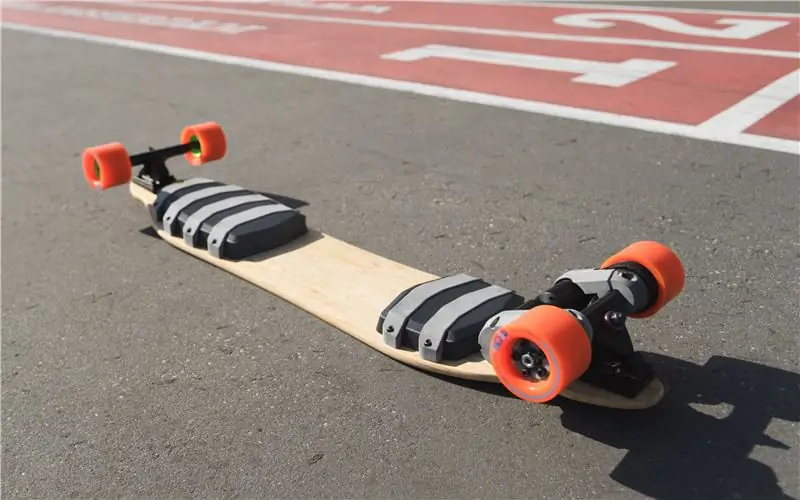
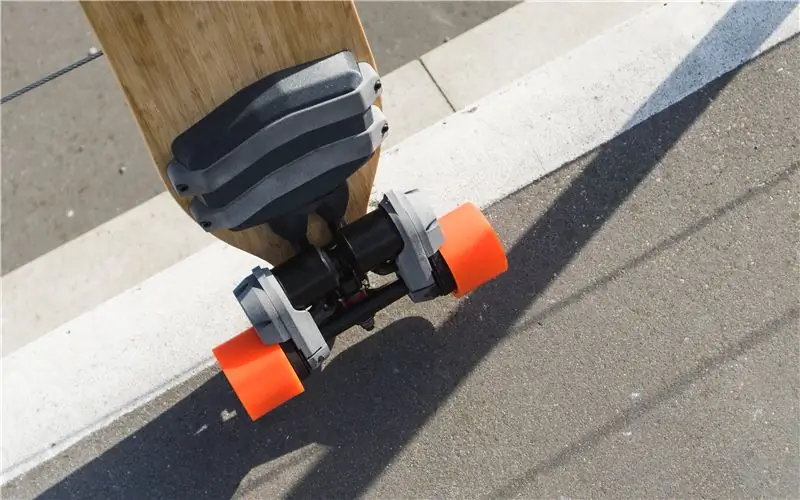
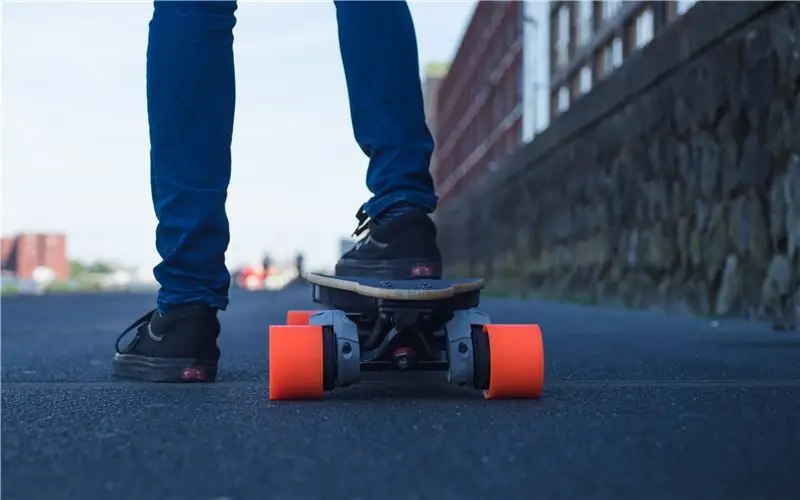
Tämä Instructable on yleiskatsaus Fusion E-Boardin rakentamisprosessista, jonka suunnittelin ja rakensin työskennellessäni 3D-keskittimissä. Hanke tehtiin 3D Hubsin tarjoaman uuden HP Multi-Jet Fusion -teknologian mainostamiseksi ja useiden 3D-tulostustekniikoiden ja niiden tehokkaiden yhdistämismahdollisuuksien esittelemiseksi.
Suunnittelin ja rakensin sähkömoottorisen longboardin, jota voidaan käyttää lyhyillä tai keskivaikeilla matkoilla tai yhdistää joukkoliikenteeseen tarjoamaan paljon laajempi matka -alue. Siinä on suuri huippunopeus, se on erittäin ketterä ja sitä on helppo kuljettaa, kun sitä ei käytetä.
Vaihe 1: Suunnitteluprosessi
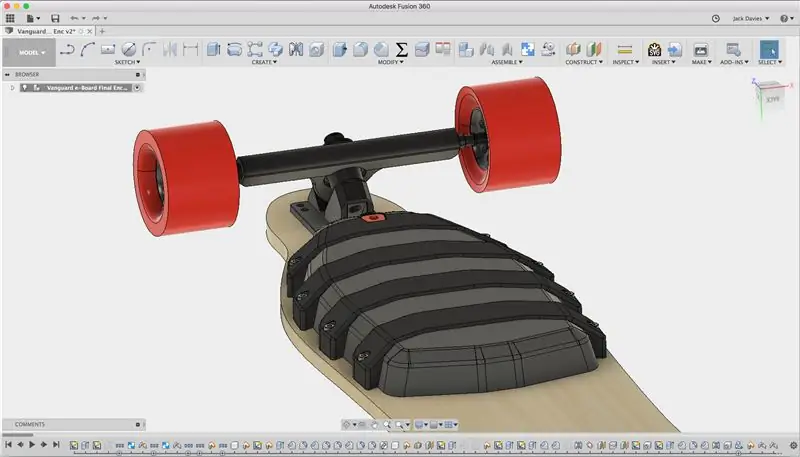
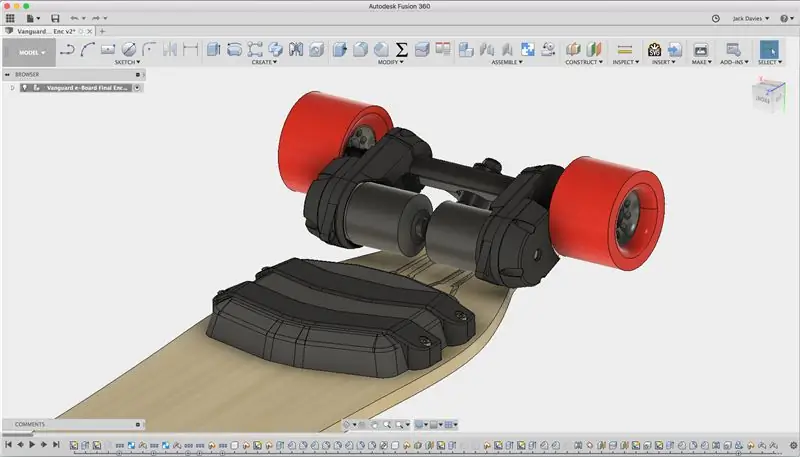
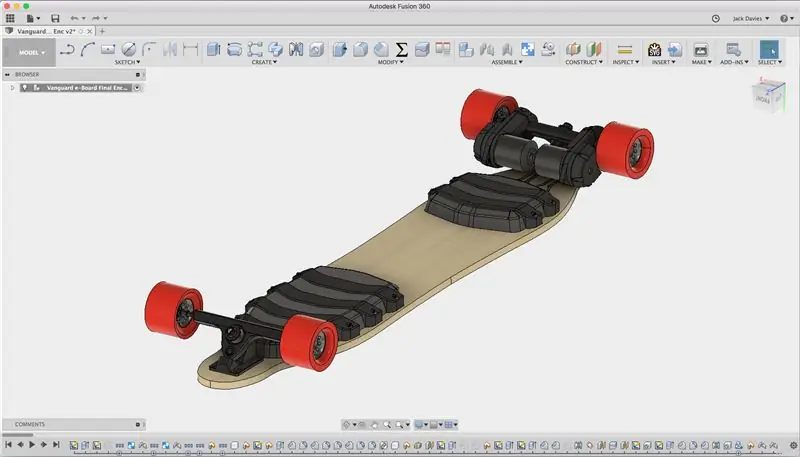
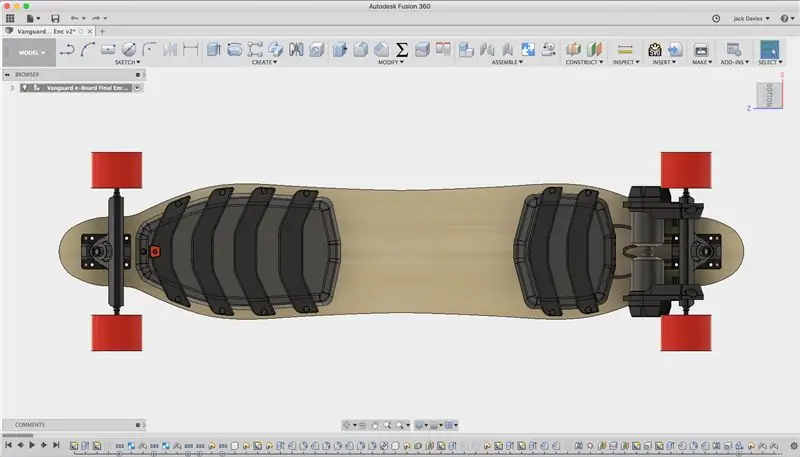
Aloitin projektin tunnistamalla longboardin pääkomponentit; kuorma -autot, kansi ja pyörät. Nämä olivat hyllyn osia, joten käytin niitä suunnittelun lähtökohtana. Ensimmäinen vaihe oli voimansiirron suunnittelu, joka sisältää moottorin kiinnikkeet, vaihteiston asennuksen ja sisälsi joitain muutoksia kuorma -autoihin. Moottorikiinnikkeiden koko ja sijainti määräävät koteloiden koon ja sijainnin, joten oli tärkeää, että tämä valmistui ensin. Laskin halutun huippunopeuden ja vääntömomentin vaatimukset, joiden avulla voin valita moottorit ja akun levylle. Myös välityssuhde laskettiin ja hihnapyörän koot sekä käyttöhihnan pituus valittiin. Näin pystyin selvittämään oikean kokoiset moottorin kiinnikkeet, jotka varmistivat hihnan kiristymisen.
Seuraava vaihe oli suunnitella akun ja nopeuden säätimen (ESC) kotelot. Valittu kansi koostuu pääasiassa bambusta, joten se on melko joustava ja taipuu huomattavasti keskellä. Tällä on etuja, koska se on mukava ajaa, koska se imee tien kolhuja eikä siirrä niitä ajajalle. Tämä tarkoittaa kuitenkin myös sitä, että akun ja elektroniikan sijoittamiseen tarvitaan jaettu kotelo, koska täyspitkä kotelo ei pystyisi taipumaan levyn kanssa ja joutuisi kosketuksiin maan kanssa käytön aikana. Elektroniset nopeudensäätimet (ESC) sijoitettiin lähinnä moottoreita sähköisten rajoitusten vuoksi. Koska moottorit on kiinnitetty kuorma -autoihin, asento muuttuu käännösten aikana, joten kotelo on suunniteltava siten, että moottorien välys on riittävä.
Akkujärjestelmä sijoitettiin kannen toiseen päähän, ja siinä oli sähköön liittyvä elektroniikka. Tähän sisältyi 20 litiumioniakkua sisältävä akku, 18650 litiumioniakku, akunhallintajärjestelmä, virtakytkin ja latauspistoke.
Käytin Autodesk Fusion360: ta koko suunnitteluprosessissa, ja tämän ohjelmiston avulla pystyin nopeasti mallinnamaan komponentteja pääyksikön sisällä, mikä nopeutti merkittävästi kehitysaikaa. Käytin myös Fusion360: n simulointiominaisuuksia varmistaakseni, että osat, erityisesti moottorin kiinnikkeet, olisivat riittävän vahvoja. Tämän ansiosta pystyin todella pienentämään kiinnikkeiden kokoa, koska voisin tarkistaa lujuus- ja taipumavaatimukset ja poistaa materiaalin säilyttäen silti asianmukaisen turvallisuustekijän. Suunnitteluprosessin jälkeen yksittäisten osien vieminen 3D -tulostusta varten oli erittäin helppoa.
Vaihe 2: Voimansiirto
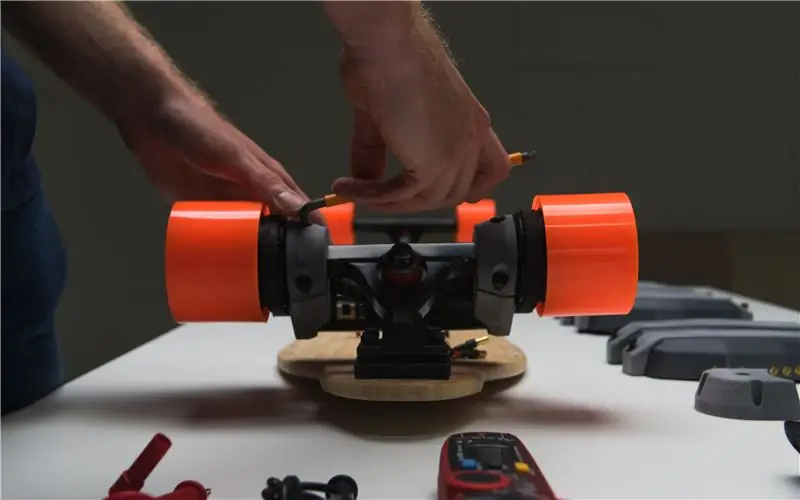
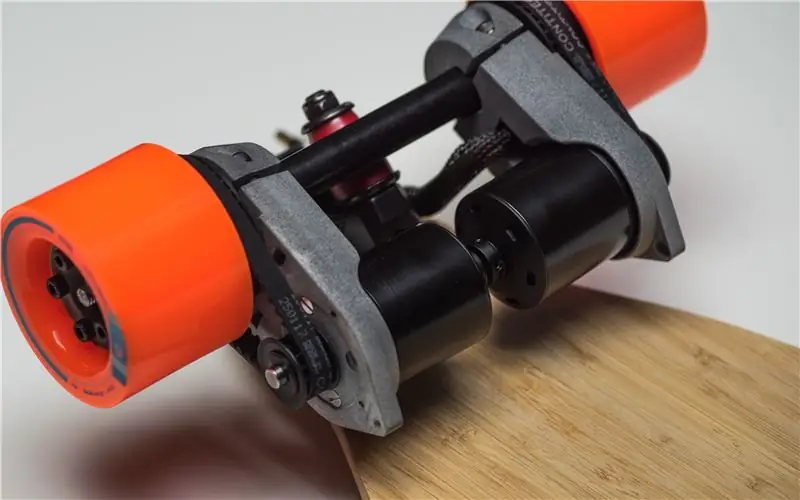
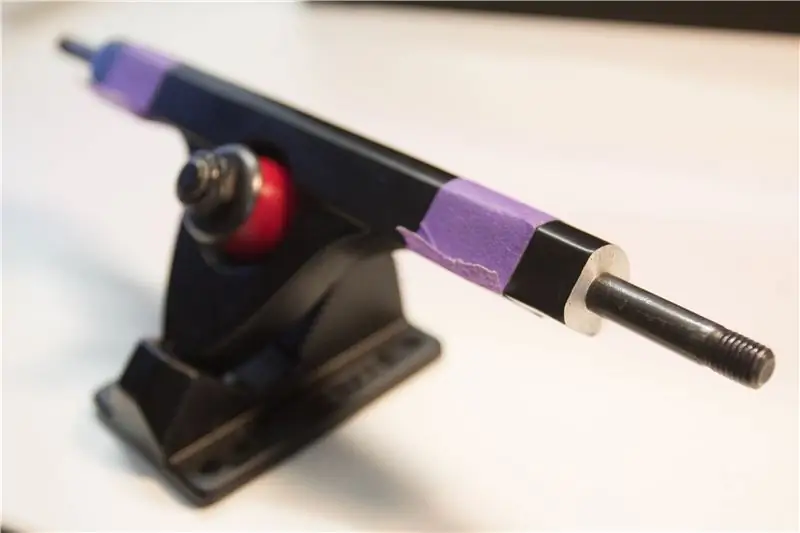
Tein ensin voimansiirron rakentamisen loppuun, jotta elektroniikkakotelolle jää riittävästi tilaa. Valitsin käytettäväksi Caliber -kuorma -autot, koska niissä on neliömäinen profiili, joka sopi täydellisesti moottorin kiinnikkeiden kiinnittämiseen. Akseli oli kuitenkin hieman liian lyhyt, jotta molempia moottoreita voitaisiin käyttää samassa kuorma -autossa, joten minun piti pidentää tätä, jotta pyörät sopisivat.
Saavutin tämän leikkaamalla osan alumiinisesta kuorma -auton ripustinrungosta paljastaen enemmän teräsakselia. Leikkasin sitten suurimman osan akselista alas, jättäen noin 10 mm, jonka voisin kiertää M8 -muotilla.
Tämän jälkeen voitiin kiinnittää kytkin ja lisätä siihen toinen kierteinen akseli, joka pidentää akselia tehokkaasti. Käytin Loctite 648 pidäteseosta kiinnittimen ja uuden akselin pysyvään kiinnittämiseen, jotta se ei ruuvaudu irti käytön aikana. Tämä salli kahden moottorin mahtuvan kuorma -autoon ja antoi runsaasti tilaa pyörille.
Voimansiirto on painettu ensisijaisesti HP Multi-Jet Fusion -tekniikalla, jotta varmistetaan jäykkyys ja lujuus suurilla kiihdytyksillä ja jarrutuksilla, joissa suurimmat voimat siirretään.
Takapyörien lukitsemiseksi suunniteltiin erityinen hihnapyörä, joka liitettiin sitten moottorin hihnapyörään HTD 5M -hihnalla. 3D -painettu kansi lisättiin hihnapyöräkokoonpanon suojaamiseksi.
Vaihe 3: Rib -kotelot
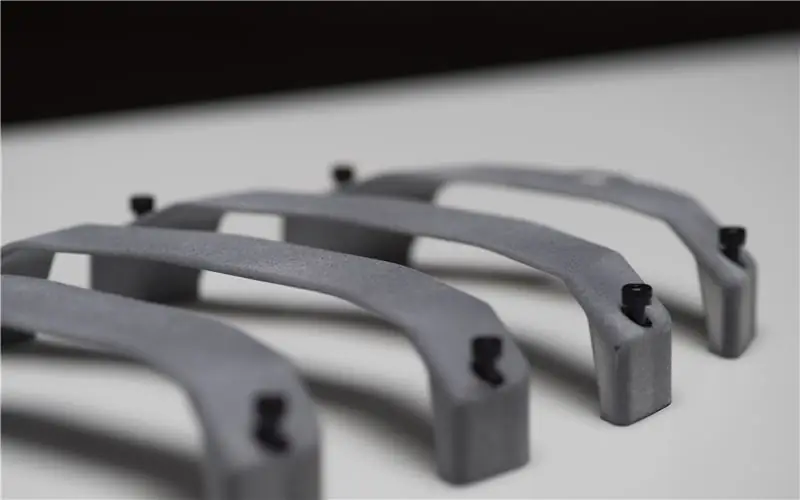
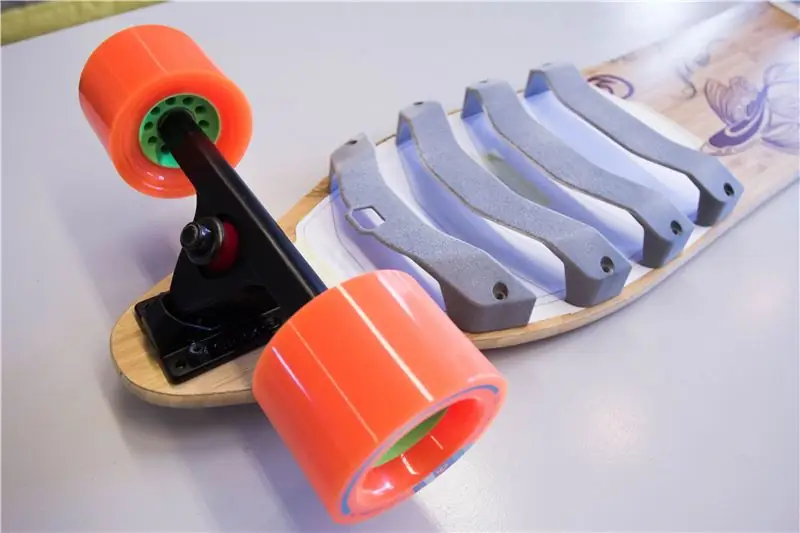
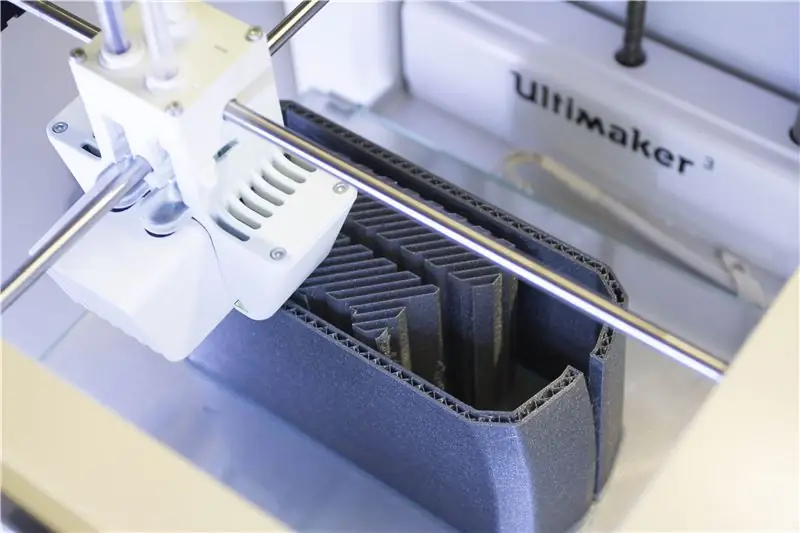
Yksi tärkeimmistä suunnittelupäätöksistäni oli koteloiden erottaminen toisistaan, mikä johti puhtaaseen ulkonäköön ja mahdollisti taipuisan kannen toiminnan ilman lisäjäykkyyttä koteloista. Halusin välittää HP Multi Jet Fusion -tekniikan toiminnalliset piirteet, joten päätin tulostaa FDM -kotelon pääosan, mikä alensi kustannuksia, ja käytin sitten HP: n osia tukemaan ja kiinnittämään ne kannelle. Tämä tarjosi mielenkiintoisen estetiikan ja oli samalla erittäin toimiva.
FDM -painetut kotelot jaettiin puoliksi tulostamisen helpottamiseksi, koska tukimateriaali voitiin poistaa ulkopinnalta. Jakolinja oli sijoitettu huolellisesti sen varmistamiseksi, että HP -osa piilotti sen, kun se kiinnitettiin levyyn. Moottoriliitäntöihin lisättiin reikiä ja kullatut luodiliittimet liimattiin paikoilleen
Kierteitetyt insertit upotettiin bambukanteen koteloiden kiinnittämiseksi levyyn, ja ne hiottiin levyn pinnan tasalle, jotta kannen ja kotelon välillä ei olisi rakoa.
Vaihe 4: Elektroniikka
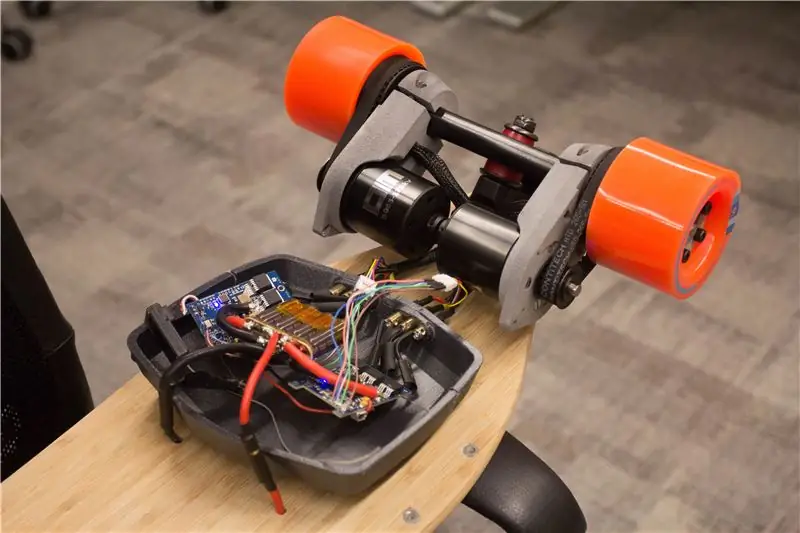
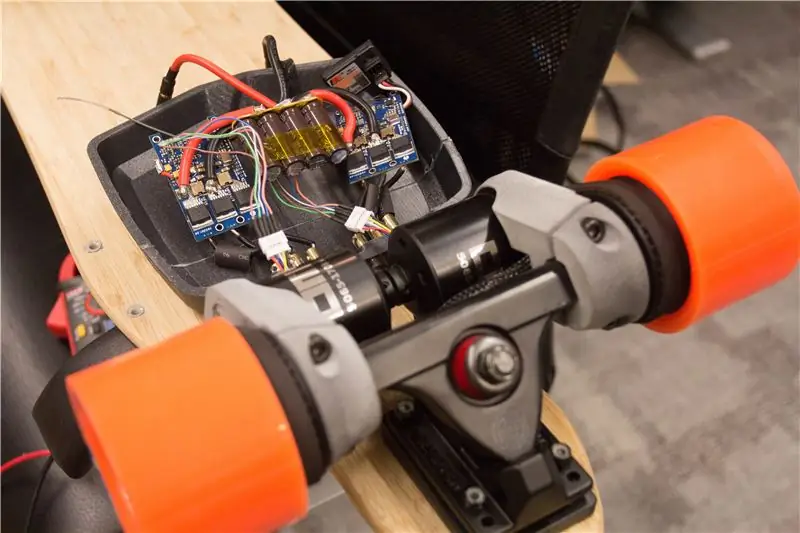
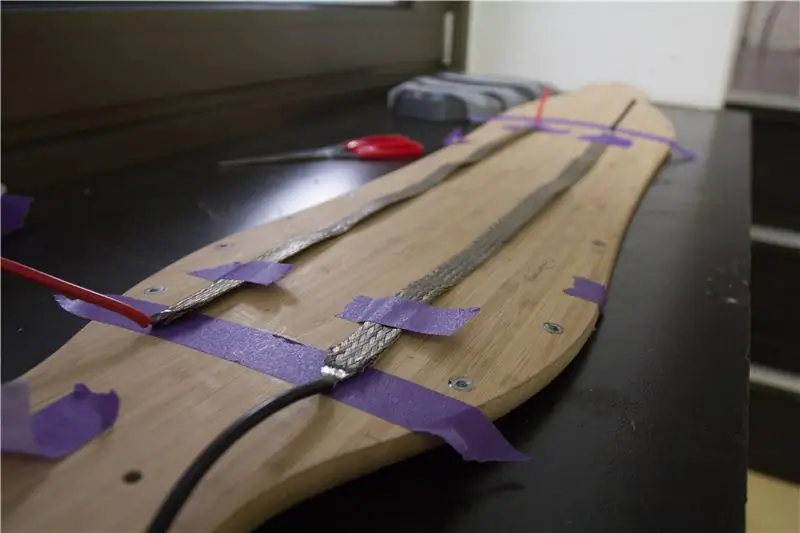
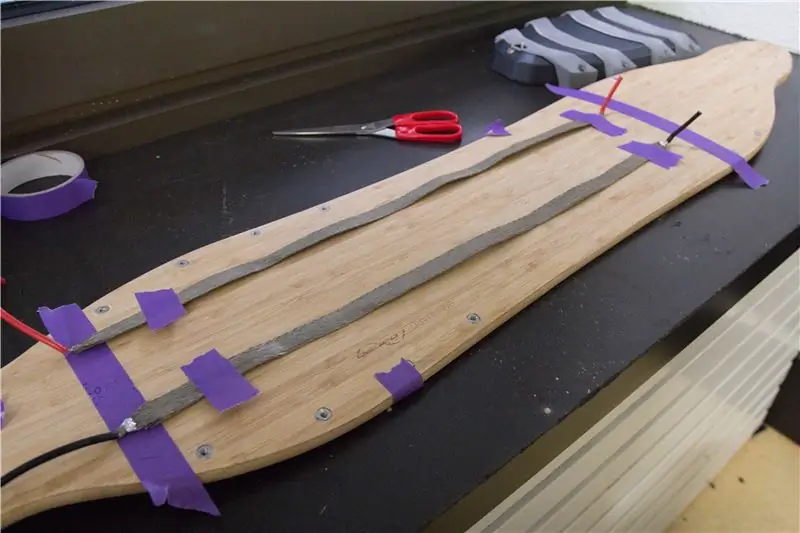
Elektroniikka on valittu huolellisesti sen varmistamiseksi, että levy on tehokas, mutta myös intuitiivinen käyttää. Tämä levy voi olla vaarallinen, jos toimintahäiriöitä ilmenee, joten luotettavuus on erittäin tärkeä tekijä.
Akku koostuu 20 yksittäisestä 18650 litiumionikennosta, jotka on hitsattu yhteen 42 V: n paketin muodostamiseksi. 2 kennoa hitsataan rinnakkain ja 10 sarjaa; käyttämäni solut olivat Sony VTC6. Hitsain nikkokielekkeitä pakkauksen muodostamiseksi pistehitsaajalla, koska juotos tuottaa liikaa lämpöä, joka voi vahingoittaa kennoa.
Akkukotelon virta siirrettiin nopeudensäätimen koteloon litteällä punotulla kaapelilla, joka vedettiin aivan kannen yläpuolella olevan teipin alle. Tämä mahdollisti kaapeleiden "piilottamisen" ja ei tarvinnut vetää kaapeleita alapuolelle, jotka olisivat näyttäneet rumailta.
Koska kyseessä on kaksimoottorinen kortti, tarvitaan kaksi nopeussäädintä jokaisen moottorin itsenäiseksi ohjaamiseksi. Käytin tähän rakenteeseen VESC -nopeussäädintä, joka on erityisesti sähköisille rullalaudoille suunniteltu ohjain, mikä tekee siitä erittäin luotettavan tähän käyttöön.
Käytetyt moottorit ovat 170kv 5065 out-runnereita, jotka voivat tuottaa 2200W kukin, mikä on paljon virtaa tällä levyllä. Nykyisellä vaihteistolla levyjen maksiminopeus on noin 35 MPH ja kiihtyy hyvin nopeasti.
Viimeinen vaihe oli luoda kauko -ohjain levyn ohjaamiseksi. Langaton järjestelmä oli edullinen helpomman käytön vuoksi. Oli kuitenkin tärkeää varmistaa lähetyksen korkea luotettavuus, koska tiedonsiirron heikkenemisellä voi olla vakavia turvallisuusongelmia etenkin suurilla nopeuksilla. Muutaman radiolähetysprotokollan testaamisen jälkeen päätin, että 2,4 GHz: n radiotaajuus olisi luotettavin tähän projektiin. Käytin hyllyltä saatavaa RC -autolähetintä, mutta pienensin kokoa merkittävästi siirtämällä elektroniikka pieneen 3D -tulostettuun käsikoteloon.
Vaihe 5: Valmis levy ja promovideo
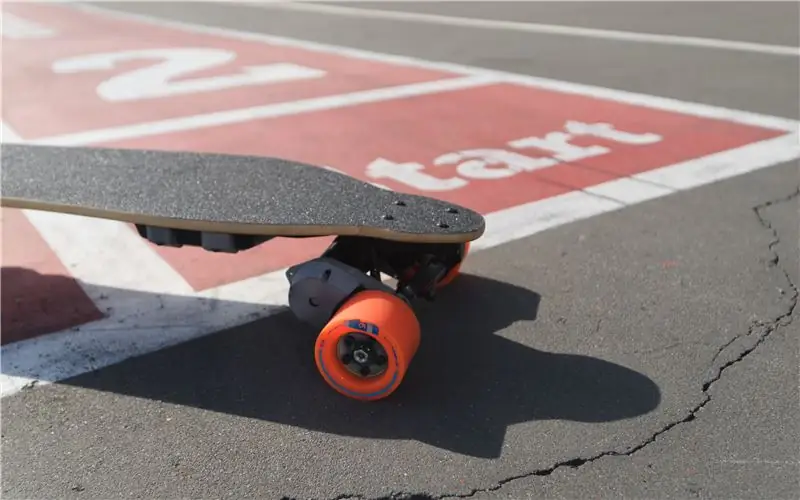
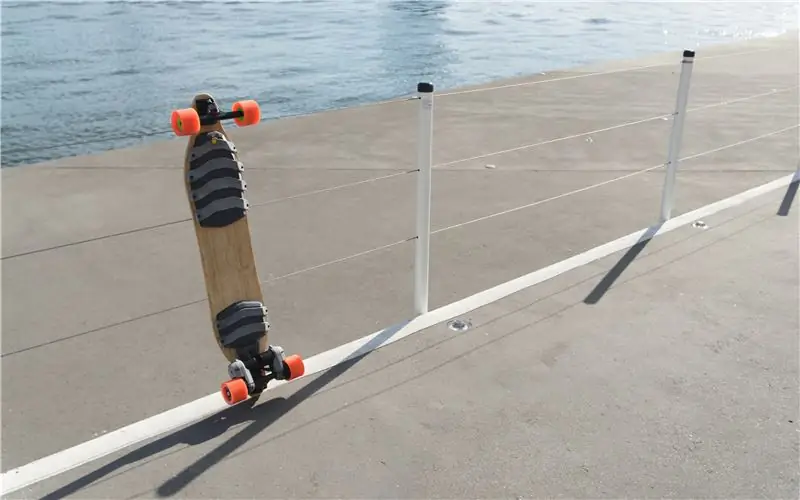
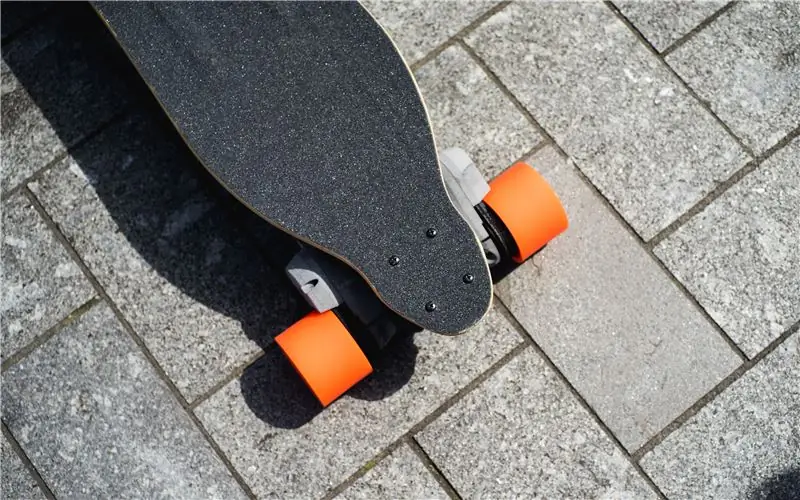
Projekti on nyt valmis! Loimme melko mahtavan videon laudasta toiminnassa, voit tarkistaa sen alta. Suuri kiitos 3D -keskittimille, jotka mahdollistivat tämän projektin toteuttamisen - katso ne täältä kaikista 3D -tulostustarpeistasi! 3dhubs.com
Suositeltava:
Nopeuslauta: Sähköinen rullalauta: 5 vaihetta
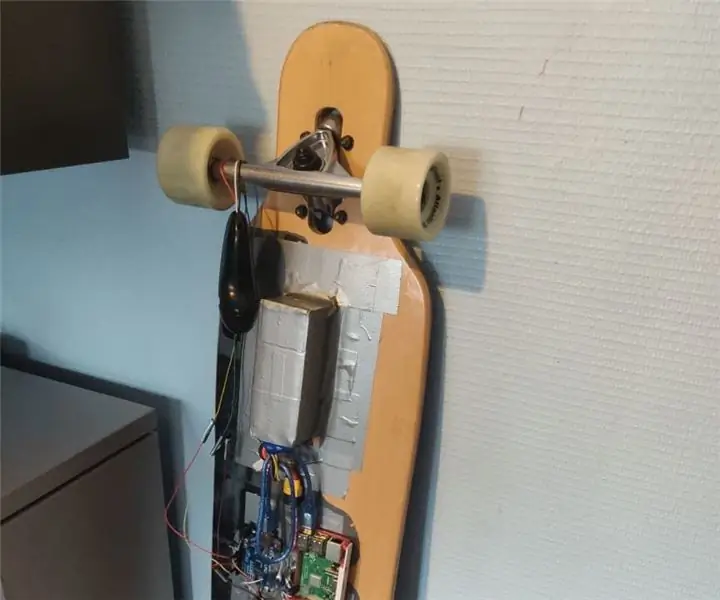
Nopeuslauta: Sähköinen rullalauta: Hei! Olen MCT College -opiskelija Howestista Belgiassa. Tänään annan sinulle vaiheittaisen oppaan siitä, miten tehdä sähköinen rullalauta vadelmapi ja arduino kanssa.
Light Graffiti -rullalauta: 6 vaihetta (kuvilla)
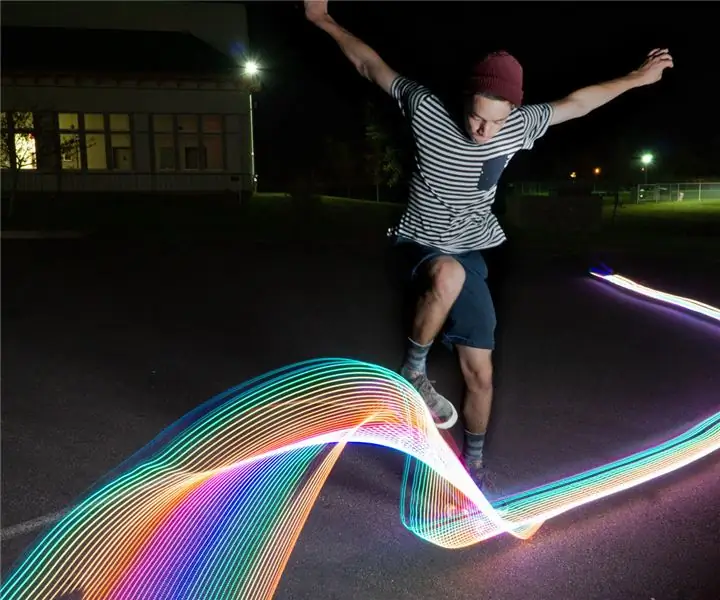
Kevyt graffiti -rullalauta: Olen tehnyt kevyitä graffiteja aiemmin, ja tulokset ja prosessi ovat aina niin hauskoja. Halusin ottaa askeleen pidemmälle ja kehittää taitojani rakentaakseni kevyt graffiti -rullalauta. Näin tein sen
Paineherkkä sähköinen rullalauta: 7 vaihetta
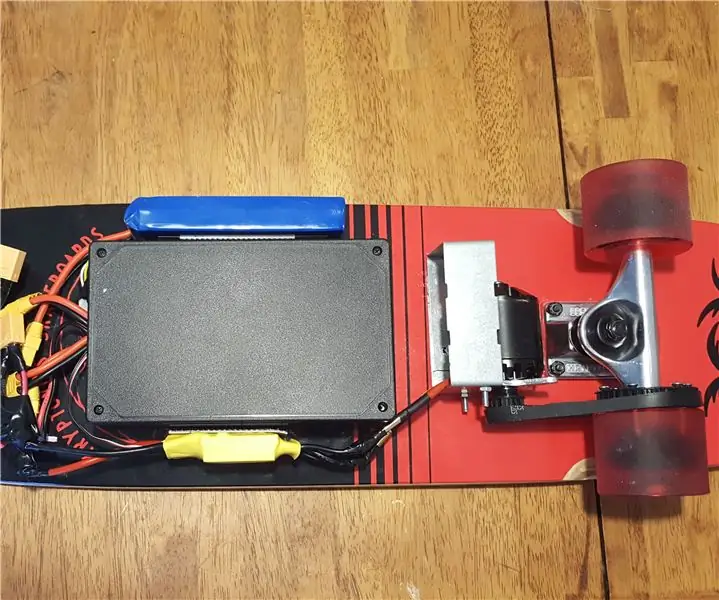
Paineherkkä sähköinen rullalauta: Tämä ohje on luotu täyttämään Etelä -Floridan yliopiston Makecourse -projektin vaatimus (www.makecourse.com). Seuraavassa ohjeessa selitetään puristusta käyttävän sähkörullalautan rakennusprosessi
OmniBoard: rullalauta- ja hoverboard -hybridi Bluetooth -ohjauksella: 19 vaihetta (kuvilla)
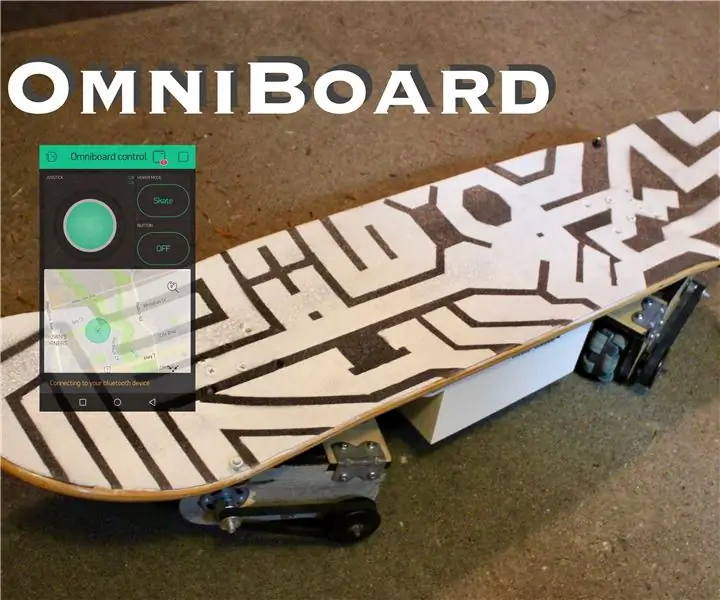
OmniBoard: rullalauta- ja hoverboard-hybridi Bluetooth-ohjauksella: OmniBoard on uusi sähköinen rullalauta-hoverboard-hybridi, jota voidaan ohjata Bluetooth-älypuhelinsovelluksen kautta. Se pystyy liikkumaan kaikilla kolmella vapausasteella, jotka molemmilla levyillä voidaan saavuttaa, mennä eteenpäin, pyöriä akselinsa ympäri ja
Rullalauta PIC -mikrokontrollerilla ja LED -valoilla: 8 vaihetta (kuvilla)
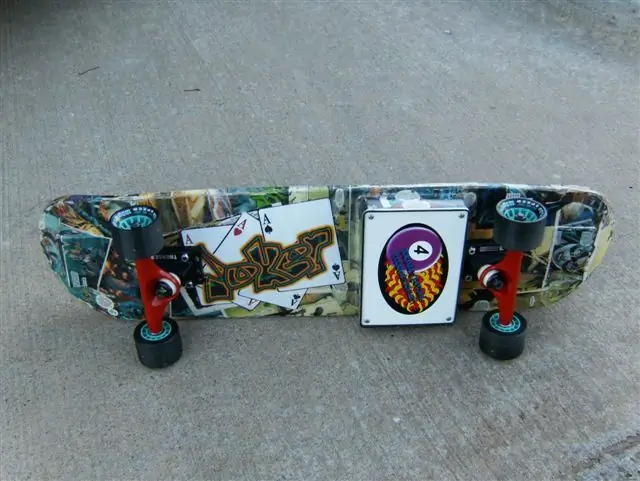
Rullalauta PIC -mikrokontrollerilla ja LED -valoilla: Mitä saat, kun sähköinsinööri rakentaa rullalaudan tyhjästä 13 -vuotiaan joululahjaksi? Saat rullalaudan, jossa on kahdeksan valkoista LEDiä (ajovalot) ja kahdeksan punaista LEDiä (takavalot), joita kaikkia ohjataan PIC -mikrokontrollerilla! Ja minä muutan